Die Casting Injection Molding: Revolutionizing Metal Fabrication
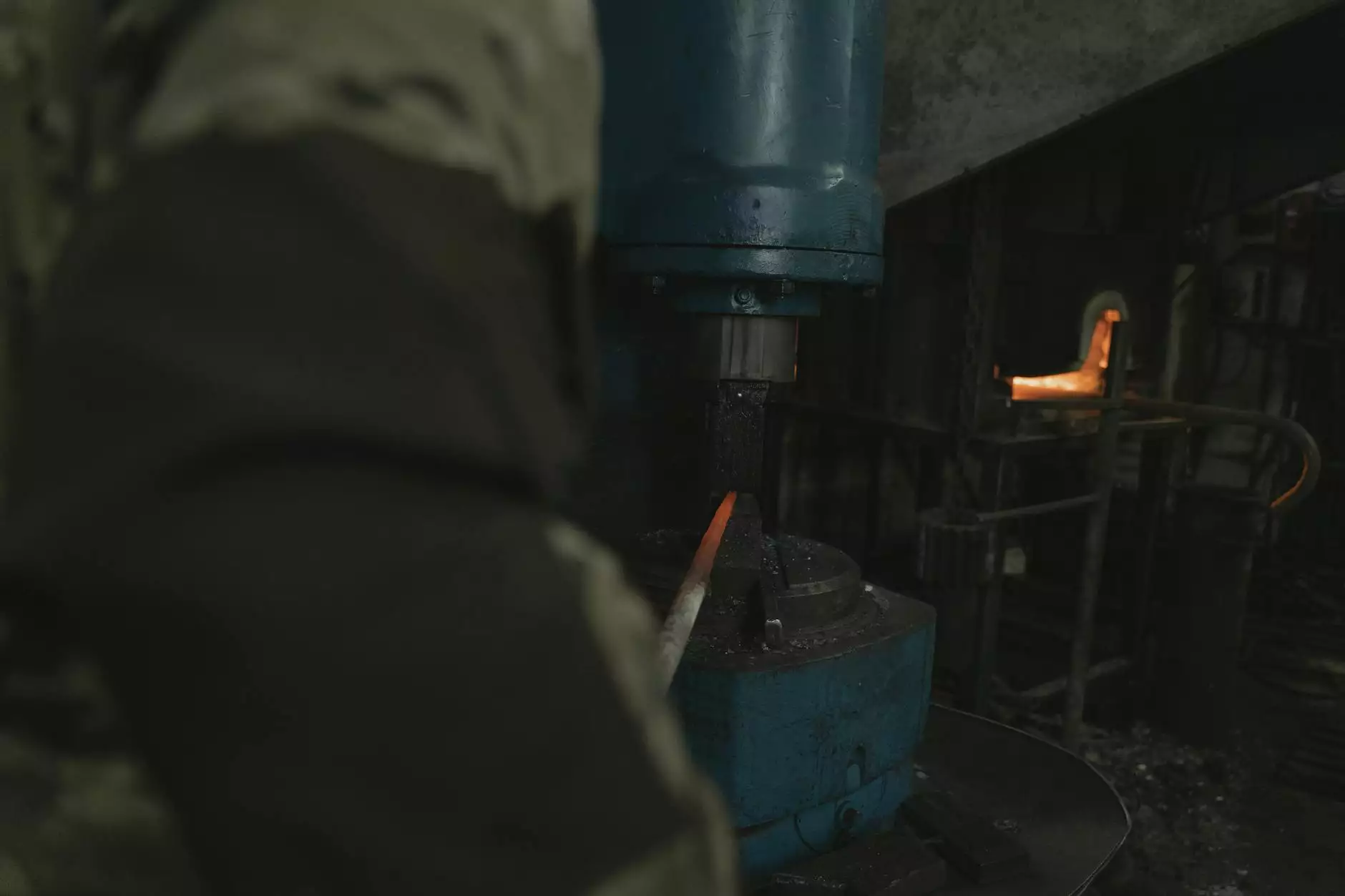
Introduction to Die Casting and Injection Molding
In the increasingly competitive landscape of manufacturing, die casting injection molding has emerged as a pivotal technology for producing high-quality metal parts with efficiency and precision. This process combines the advantages of both die casting and injection molding, allowing metal fabricators to achieve superior results.
Understanding the Basics
Before delving deeper into the intricacies of die casting injection molding, it’s essential to understand what each component entails:
- Die Casting: This is a metal casting process that forces molten metal into a mold cavity under high pressure. The molds are usually made of hardened steel to withstand the extensive pressure and heat involved.
- Injection Molding: A manufacturing process for producing parts by injecting molten material into a mold. This can apply to metals, plastics, and other materials, providing flexibility in fabrication.
The Die Casting Injection Molding Process
The die casting injection molding process is a sophisticated integration that allows manufacturers to create complex shapes with high dimensional accuracy. Here’s how the process typically unfolds:
- Preparation of Metal Alloys: The process begins with the selection of suitable metal alloys, commonly aluminum, zinc, or magnesium, known for their lightweight and durability.
- Heating and Injection: The selected metal alloy is heated to its melting point, after which it is injected into a pre-prepared mold using a specialized machine, applying high pressure to ensure the mold is filled completely.
- Cooling and Solidification: After the injection, the molten metal cools rapidly within the mold, solidifying into the desired shape.
- Demolding: Once cooled, the part is ejected from the mold. The precision of the mold ensures that minimal post-processing is needed.
Benefits of Die Casting Injection Molding
The integration of die casting and injection molding brings forth numerous advantages for metal fabricators:
- High Precision and Accuracy: The precision of molds used in die casting injection molding ensures that parts are produced with minimal tolerance, which is crucial in many industrial applications.
- Cost-Effectiveness: This method allows for high-volume production runs, reducing the cost per unit significantly while maintaining quality.
- Complex Geometries: Manufacturers can create intricate designs that are difficult or impossible to achieve with traditional machining processes.
- Material Efficiency: The process minimizes waste by utilizing the exact amount of material required to produce each part.
Applications of Die Casting Injection Molding
The versatility of die casting injection molding makes it suitable for a wide range of applications across various industries:
- Automotive Industry: Components such as engine blocks, transmission housings, and wheels benefit from lightweight yet strong properties provided by this manufacturing technique.
- Electronics: Enclosures, housings, and intricate parts for electronic devices can be produced with high precision and aesthetic appeal.
- Aerospace: Aerospace components need to adhere to strict safety standards while maintaining a lightweight structure; die casting serves this requirement excellently.
- Consumer Products: Many household items, tools, and appliances utilize parts manufactured through this process, ensuring they are durable and cost-effective.
Environmental Considerations
In today’s eco-conscious world, sustainability in manufacturing is paramount. The die casting injection molding process contributes to environmental protection in several ways:
- Reduced Waste: The precision of the process means less scrap material is generated, promoting a more sustainable approach to metal fabrication.
- Energy Efficiency: Advances in die casting technology have led to machines that consume less energy while maintaining high output rates.
- Recyclability of Materials: Many of the metals used in this process, particularly aluminum and zinc, are highly recyclable, allowing for closed-loop production cycles.
Choosing the Right Die Casting Injection Molding Partner
When it comes to selecting a partner for die casting injection molding, it’s vital to consider several factors to ensure you are making the best choice for your manufacturing needs:
- Experience and Expertise: Look for a manufacturer with a proven track record in the industry, capable of delivering quality results consistently.
- Technology and Equipment: Ensure the company invests in modern, high-tech machines that meet the latest standards in precision and efficiency.
- Customer Support: A dependable partner will provide excellent support and communication throughout the manufacturing process.
- Quality Assurance: Verify that they have rigorous quality control measures in place to guarantee the integrity of the final products.
Future Trends in Die Casting Injection Molding
The landscape of die casting injection molding is continually evolving. Here are some future trends that businesses should watch for:
- Enhancements in Automation: As technology advances, more processes in die casting will become automated, leading to faster production speeds and reduced labor costs.
- Integration of Smart Manufacturing: The incorporation of IoT and smart manufacturing principles will enable real-time monitoring, optimizing production processes.
- New Alloy Development: Research into new metal alloys that improve performance and reduce costs is ongoing, promising even more innovative applications.
- Sustainability Initiatives: Growing pressure to reduce the carbon footprint will drive further investments in energy-efficient technologies and materials.
Conclusion
In conclusion, die casting injection molding is a transformative process that has significantly impacted the world of metal fabrication. By combining precision, efficiency, and sustainability, it offers manufacturers the tools they need to excel in a competitive market. Whether in the automotive, aerospace, electronics, or consumer goods industries, this process is paving the way toward innovation and excellence in production.
Companies like DeepMould.net are at the forefront of this transformation, leveraging their expertise in metal fabrication to create solutions that not only meet but exceed industry standards. Embracing die casting injection molding technology can lead to remarkable advancements in manufacturing, turning ideas into reality with speed and precision.