Understanding Manifold Valve Working: A Comprehensive Guide
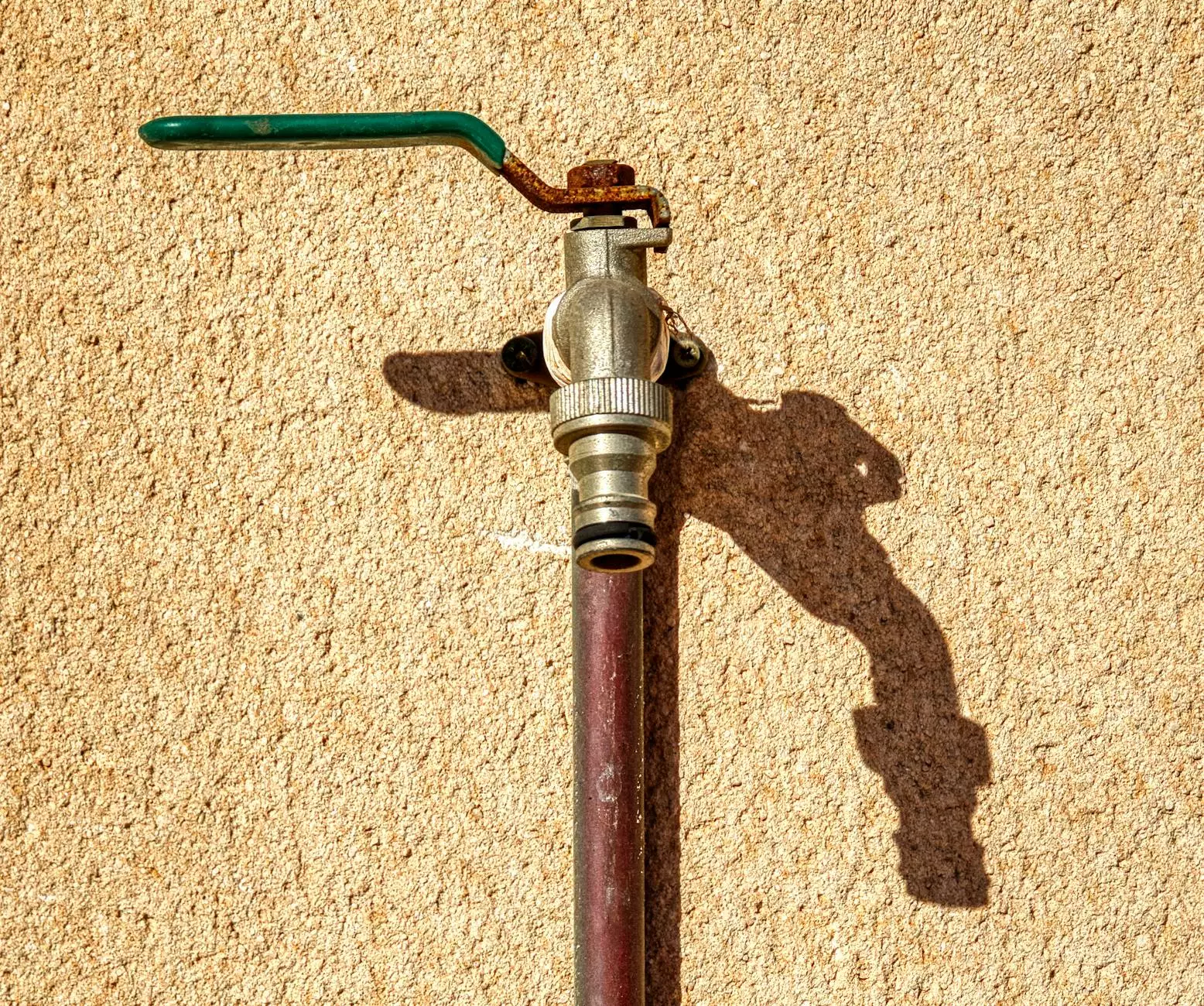
Introduction to Manifold Valves
Manifold valves are essential components in many fluid control systems. They serve as a critical link in hydraulic and pneumatic systems by directing and regulating the flow of fluids. Understanding the manifold valve working mechanism is crucial for engineers, technicians, and anyone involved in system design and maintenance. This article delves into the operational principles, types, applications, and benefits of manifold valves, providing a comprehensive insight into their functionality.
What is a Manifold Valve?
A manifold valve is designed to channel multiple flows of fluid through a single body, allowing for efficient management of flow rates and pressure. Typically composed of several ports and valves integrated into a single unit, manifold valves reduce the complexity and potential leak points in a hydraulic or pneumatic system.
How Do Manifold Valves Work?
The fundamental principle of manifold valve working revolves around controlling the path of fluid flow. Here's how it operates:
- Fluid Entry: Fluid enters the manifold through a designated inlet port.
- Flow Direction Control: Based on the position of the control mechanism (which could be manual or automated), the valve directs the fluid to one or more outlet ports. This is achieved through internal passages or chambers within the manifold body.
- Pressure Regulation: Many manifold valves include features for pressure control, ensuring that the fluid is delivered at the correct pressure levels to various components.
- Fluid Exit: Finally, the fluid exits through the selected outlet port, delivering it to the desired destination within the hydraulic or pneumatic system.
Types of Manifold Valves
Various types of manifold valves exist, tailored for specific applications. Here are some of the most common types:
- 5-Way Manifold Valves: Typically used in gas and liquid applications, these valves provide connection options for various configurations.
- 4-Way Manifold Valves: Often employed in directional control applications, allowing for bidirectional flow control.
- Needle Manifold Valves: Designed for precise flow control, needle valves allow for fine adjustments in fluid flow.
- Ball Manifold Valves: Featuring a spherical disc, these valves allow for quick on/off control.
Applications of Manifold Valves
Manifold valves find extensive applications across various industries, including:
- Hydraulic Systems: Used to control hydraulic flow and pressure in heavy machinery and automotive applications.
- Pneumatic Systems: Essential for directing airflow in applications ranging from industrial automation to medical devices.
- Oil and Gas Industry: Manifold valves play a critical role in managing the flow of both liquid and gas hydrocarbons.
- Chemical Processing: Allowing precise control over the mixing and transfer of chemicals.
Benefits of Using Manifold Valves
Incorporating manifold valves in a system design can yield several advantages, such as:
- Space Efficiency: With multiple valves integrated into a single manifold, required installation space is minimized.
- Reduced Leakage: Fewer connection points generally lead to reduced chances of leaks.
- Cost-Effectiveness: Lower overall manufacturing and installation costs due to fewer individual components.
- Enhanced Performance: Improved flow dynamics often lead to increased system performance and reliability.
Choosing the Right Manifold Valve
Selecting the appropriate manifold valve for any application involves several considerations:
- Fluid Type: Ensure the valve material can withstand the specific fluid being used.
- Pressure Ratings: Verify the pressure requirements of your system to prevent failures.
- Size and Configuration: Determine the right size and port configuration for optimal performance.
- Temperature Limits: Consider the operating temperature range of the fluids involved.
Innovations in Manifold Valve Design
Like many industries, the manifold valve sector is experiencing technological advancements. Innovations include:
- Smart Manifolds: Integrated sensors that allow for real-time monitoring and adjustments.
- 3D Printing: Enhanced customization of manifolds using additive manufacturing for specific applications.
- Improved Materials: Development of advanced materials that offer better resistance to corrosion and wear.
Maintenance of Manifold Valves
Regular maintenance is crucial to ensure the longevity and proper functioning of manifold valves. Key maintenance practices include:
- Visual Inspections: Regularly examine for signs of wear, corrosion, or leaks.
- Cleaning: Ensure that valves are kept free from debris and contaminants.
- Testing: Periodically test the valve’s performance and functionality.
- Replacement of Worn Parts: Replace seals, gaskets, and other components as needed to maintain optimal performance.
Conclusion
Understanding the manifold valve working mechanism is essential for optimizing fluid management in a variety of industrial applications. By leveraging the unique advantages of manifold valves, businesses can achieve greater efficiency, reduce costs, and enhance system reliability. With ongoing innovations in design and technology, the future of manifold valves looks promising, opening new possibilities for improved fluid control solutions in diverse sectors.
For more information on manifold valves and related products, visit TechTubes.in.