The Integral Role of Die Casting Mold Suppliers in Today's Manufacturing
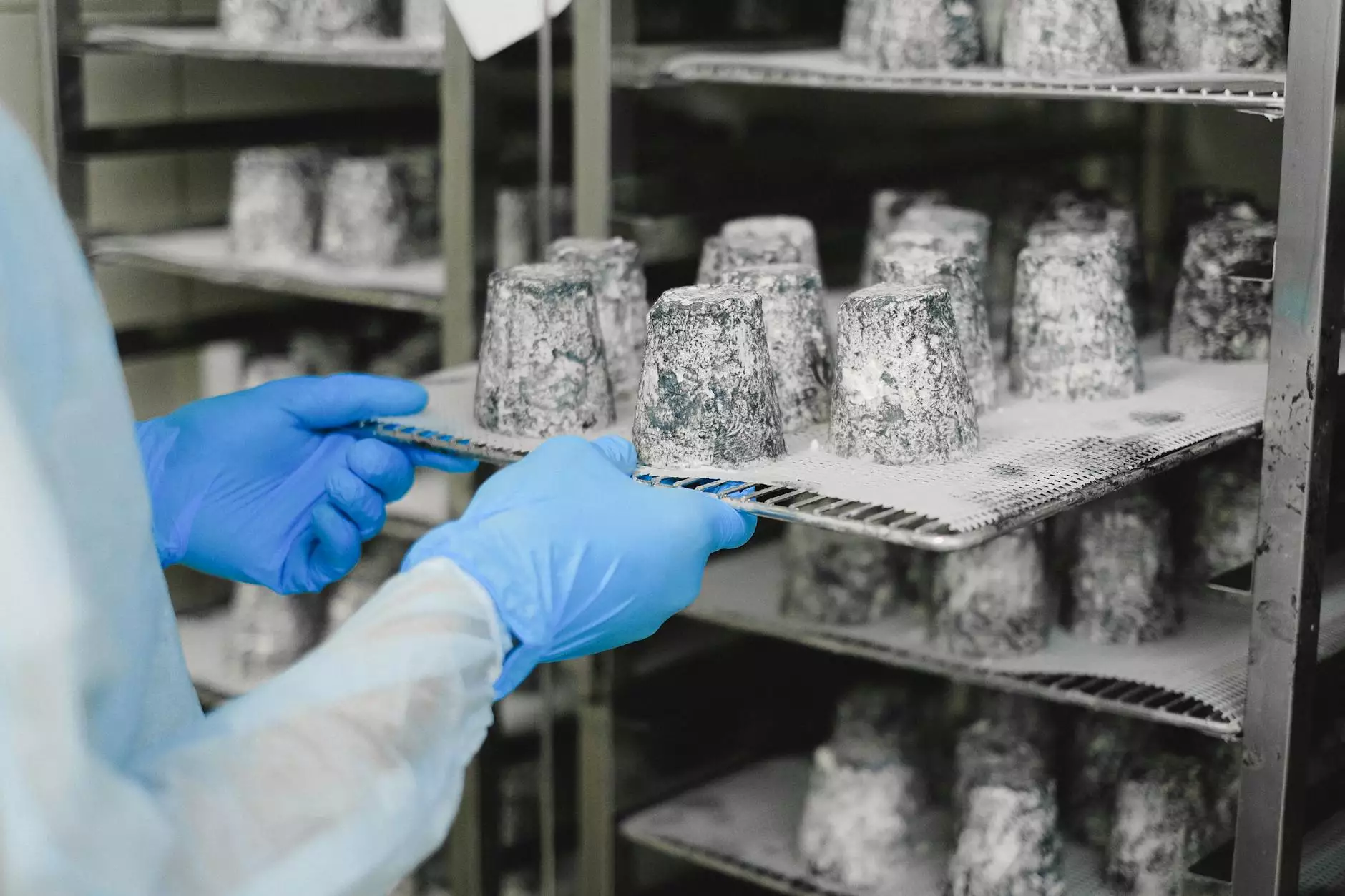
What is Die Casting?
Die casting is a manufacturing process that involves forcing molten metal into a mold cavity under high pressure. The process is highly efficient and allows for the production of complex shapes with excellent surface finish and dimensional accuracy. The molds, commonly known as die casting molds, play a vital role in this process and are key to achieving high-quality end products.
Importance of Die Casting Mold Suppliers
To ensure the successful implementation of the die casting process, the choice of a qualified die casting mold supplier is crucial. These suppliers provide not only the molds but also technical support and expertise that can significantly impact manufacturing efficiency and product quality.
Key Responsibilities of a Die Casting Mold Supplier
- Design Expertise: Suppliers should offer customized mold designs that meet specific product requirements.
- Quality Materials: They utilize high-grade materials to ensure durability and longevity of the molds.
- Advanced Manufacturing Techniques: Employing the latest technology in mold production enhances precision and reduces lead times.
- Technical Support: Providing guidance and problem-solving solutions throughout the production process.
Benefits of Working with a Reliable Die Casting Mold Supplier
Partnering with a reputable die casting mold supplier offers several distinct advantages that can enhance your overall production capabilities:
1. Enhanced Production Efficiency
Using high-quality molds developed by experienced suppliers leads to fewer defects and decreased cycle times, allowing manufacturers to produce more parts in less time.
2. Cost-Effectiveness
While the initial investment in quality molds may be higher, the long-term savings from reduced scrap rates and improved productivity often outweigh these costs.
3. Versatility
Good suppliers can produce molds for a wide range of alloys and applications, ensuring that manufacturers can adapt to market changes without switching suppliers frequently.
4. Innovation and Technology Transfer
Suppliers often invest in research and development. By collaborating with these suppliers, manufacturers can leverage new technologies and innovations that can improve their product offerings.
How to Choose the Right Die Casting Mold Supplier
When selecting a die casting mold supplier, consider the following critical factors:
1. Experience and Reputation
Look for suppliers with a proven track record in the die casting industry. Research their client testimonials and case studies to gauge their reliability and expertise.
2. Technical Capabilities
Evaluate their design and manufacturing capabilities. Ask about their design software, machinery, and prototyping processes.
3. Quality Assurance Processes
Ensure they have robust quality control measures in place. Certifications like ISO 9001 can indicate a commitment to maintaining high standards.
4. Customer Support
A strong support network can make a significant difference. Ensure the supplier provides comprehensive technical support and timely communication.
5. Cost and Value Analysis
While cost is an important consideration, it should not be the sole factor. Assess the value provided in terms of quality, support, and long-term savings.
Applications of Die Casting Across Industries
Die casting is versatile and widely used across many industries, including:
- Automotive: Components such as engine blocks, transmission cases, and decorative trims.
- Aerospace: Lightweight and complex components designed for airframes and engines.
- Consumer Electronics: Housings and components found in electronic devices and appliances.
- Furniture and Fixtures: Decorative and functional hardware in furniture design.
The Future of Die Casting and Mold Suppliers
As technology evolves, the die casting industry is also moving towards greater efficiency and sustainability. The role of a die casting mold supplier is expected to transform with innovations such as:
1. 3D Printing
With advancements in 3D printing, suppliers can prototype and adjust mold designs more rapidly than before, facilitating faster turnaround times.
2. Smart Manufacturing
The integration of IoT (Internet of Things) in manufacturing processes allows for better monitoring and optimization of die casting operations.
3. Sustainable Practices
As sustainability becomes a priority, suppliers are focusing on materials and processes that minimize environmental impact, including recycling metals and reducing energy use during production.
Make the Right Choice with DeepMould
DeepMould, a leading die casting mold supplier, offers unparalleled expertise and a commitment to quality. Their products are designed to excel in various applications, ensuring that you receive the best solutions tailored to your needs. With a focus on innovation, quality assurance, and customer support, DeepMould remains the go-to partner for metal fabricators looking to enhance their production capabilities.
Conclusion
In conclusion, the importance of selecting a reliable die casting mold supplier cannot be overstated. As industries evolve, so too do the demands for quality, efficiency, and sustainability. By partnering with a supplier like DeepMould, manufacturers can gain a competitive edge and ensure their products meet the highest standards of quality and performance.